In the current fast-paced manufacturing landscape, the quest for effectiveness and swiftness has become crucial. Companies are constantly seeking methods to reduce turnaround times and enhance production processes, and one method that has emerged as a game-changer is rapid injection molding. This cutting-edge technique is revolutionizing the way products are developed and brought to market, enabling manufacturers to respond to consumer demand with unprecedented agility.
Rapid injection molding not only streamlines the production process but also significantly reduces costs associated with conventional manufacturing methods. By utilizing advanced technologies and materials, manufacturers can create top-notch prototypes and production parts in a much shorter duration. This ability to quickly modify and refine designs enables businesses to stay competitive, meet tight deadlines, and deliver exceptional products to their customers. As the demand for faster and more efficient manufacturing solutions keeps to grow, rapid injection molding stands out as a valuable tool that manufacturers cannot afford to overlook.
Advantages of Rapid Injection Molding
Fast injection molding provides manufacturers a distinct blend of quickness and efficiency that sets it apart from traditional injection molding techniques. One of the main advantages is the greatly reduced lead time for manufacturing molds and parts. While conventional methods may need several weeks or even months to get a mold finished, fast injection molding streamlines this process, often accomplishing it in a matter of days. This effectiveness allows companies to bring products to market sooner, offering them a competitive edge in dynamic industries.
Additionally, benefit is the cost-effectiveness of rapid injection molding for small to medium production runs. Conventional molding can incur high initial costs associated with mold creation, which renders it less feasible for limited production quantities. In contrast, the fast approach utilizes advanced technologies and materials that reduce costs without jeopardizing quality. This positions it as an optimal solution for businesses looking to test products or tailor items without significant financial commitment.
Finally, fast injection molding enables enhanced flexibility and design freedom. Companies can conveniently make modifications to their designs due to the quicker turnaround times related with rapid processes. This flexibility allows for continuous testing and feedback, ultimately leading to enhanced product designs and greater customer satisfaction. With rapid injection molding, manufacturers can react to market needs swiftly, making sure they stay relevant and in the game.
Uses in Various Industries
Quick injection molding has demonstrated to be an integral tool for different industries, significantly enhancing their manufacturing processes. In the vehicle sector, for instance, manufacturers utilize quick injection molding to create intricate parts and components in a small portion of the time it typically takes. This speed not only speeds up the development cycle of innovative vehicles but also allows for swift adjustments to designs based on consumer needs, ultimately leading to increased competitiveness.
The healthcare industry also gains substantially from rapid injection molding. With strict regulations and a continuous need for precision, medical device manufacturers turn to this method for producing essential components such as housings and connectors. Rapid injection molding enables these manufacturers to produce prototypes quickly, facilitating quicker testing and compliance with safety standards, which is crucial in the medical field.
Moreover, the customer products sector has adopted quick injection molding to meet rapidly evolving consumer preferences. Companies in this sector can swiftly produce short batches of bespoke products or limited editions, adapting to market trends almost in real-time. This capability to innovate and bring products to market swiftly gives them a substantial advantage over competitors who rely on traditional manufacturing methods.
Future Trends and Innovations
As endeavor to explore ways to boost efficiency and minimize costs, the field of rapid injection molding is poised to evolve remarkably. Emerging technologies including AI and machine learning are starting to have a key role in enhancing the design and production processes. These developments can yield better precision in mold design, real-time monitoring of production parameters, and quicker adjustments to the manufacturing process. As a result, companies can expect reduced lead times and more efficient production cycles while maintaining high quality standards.
Additionally, an interesting trend is the incorporation of green practices within rapid injection molding. As awareness of environmental impacts expands, manufacturers are progressively looking to incorporate biodegradable options and recyclable materials into their manufacturing processes. Advances in material science are resulting in a broader range of sustainable polymers, allowing companies to meet consumer demands for green solutions without compromising functionality. This change not only promotes environmental responsibility but also creates new markets for manufacturers adopting greener solutions.
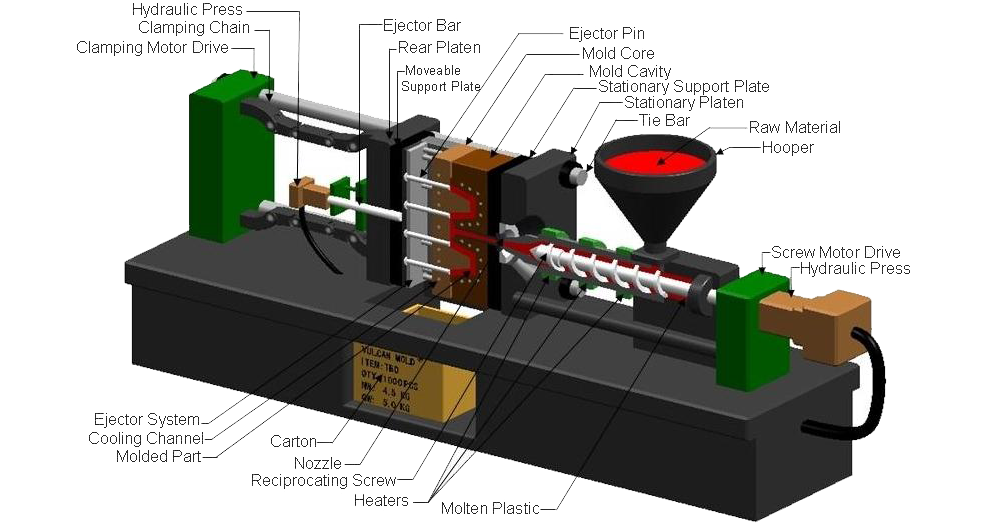
Lastly, the future of the field may also see enhanced customization options. As the rise of on-demand manufacturing and the drive for customized solutions, businesses can utilize rapid injection molding to develop bespoke products that meet distinct customer needs. This versatility not only enhances customer satisfaction but also establishes manufacturers as flexible players in a competitive market. As technology continues to advance, the potential for this technology to adapt and make advancements will be a significant driver of its success in the manufacturing landscape.